بحث در مورد استفاده بهینه از انرژی در بسیاری از بخشهای صنعت رایجتر شده است. ماشین ابزار شامل موتورهای متعدد و اجزای کمکی است که مصرف انرژی آنها می تواند در حین ماشینکاری به شدت متفاوت باشد. به عنوان مثال، درایو اسپیندل اصلی و سیستم خنککننده در حین زبر کردن با نرخ حذف بالا، نزدیک به توان نامی خود کار میکنند، در حالی که مصرف برق در حین تکمیل به طور قابلتوجهی کمتر است. وابستگی متقابل بسیار نزدیکی بین تک تک اجزا و مجموعه های فرعی یک ماشین ابزار و جنبه های بهره وری و کیفیت وجود دارد. از بررسی دقیق فرآیندهای تولید گرفته تا مصرف برق تک تک اجزا، پتانسیل صرفه جویی را می توان ارزیابی کرد و اقداماتی را برای استفاده بهینه از انرژی تعریف کرد.
در بسیاری از شاخه های صنعت کالاهای سرمایه گذاری، بهره وری انرژی به یک ویژگی مهم محصول تبدیل شده است. موتورهای دنده ای برای فناوری جابجایی مواد مدتی است که به کلاس های بازده تقسیم می شوند. ایده های زیادی برای افزایش بهره وری انرژی در تولید با ماشین ابزار آزمایش شده است. صرفه جویی بالقوه با توجه به بار پایه ماشین ابزار که نیاز به مصرف انرژی حتی در فازهای غیرمولد دارد، حاصل می شود. بار پایه اساساً توسط اجزای کمکی یک ماشین تعیین می شود. علاوه بر استفاده از موتورهای کم مصرف در اجزای کمکی، امکانات زیادی برای کاهش بار پایه در مدیریت صحیح انرژی یافت می شود. با مدیریت انرژی، مصرف کنندگان به طور خاص توسط کنترل ماشین در مراحل غیرمولد خاموش می شوند.
اقدامات پشتیبانی از اپراتور در حین راه اندازی همچنین باعث افزایش بهره وری انرژی می شود، زیرا آنها فازهای غیرمولد را کوتاه می کنند و تأثیر بار پایه را کاهش می دهند. قراضه به طور اجتناب ناپذیری مصرف انرژی را برای هر قطعه خوب افزایش می دهد. بنابراین ساخت با دقت از همان قسمت اول می تواند به یک عامل تعیین کننده برای بهره وری انرژی یک ماشین ابزار تبدیل شود. طراحی ماشینها با رفتار حرارتی متعادل و فناوری اندازهگیری موقعیت دقیق ، مزیت مشخصی در اینجا دارند.
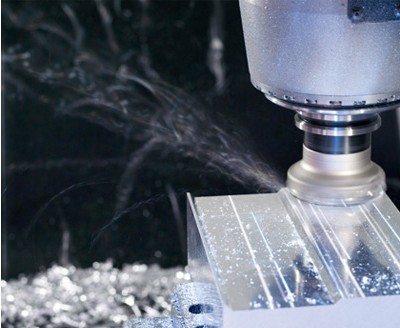
تقاضای انرژی در طول آسیاب
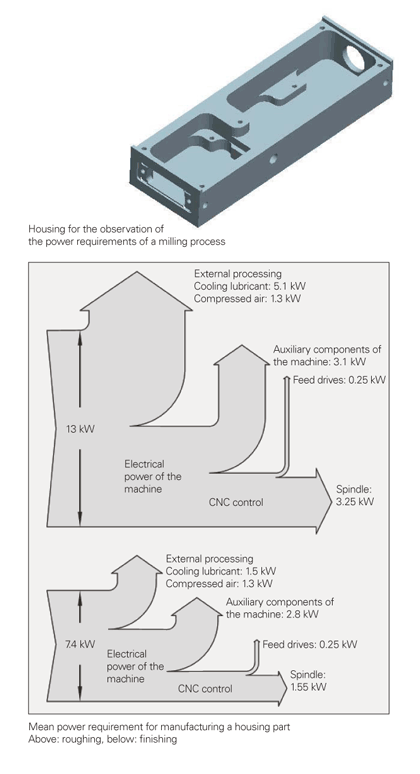
توان مورد نیاز فرآیند آسیاب به گروه های مصرف کننده زیر تقسیم می شود:
- پردازش روان کننده خنک کننده
- تولید هوای فشرده
- اجزای کمکی دستگاه فرز با نیروی برق
- پکیج کنترل CNC با دوک اصلی و موتورهای محور تغذیه
انرژی محاسبه شده متناسب برای روشنایی، تهویه و تهویه مطبوع به این گروه ها اضافه می شود. نیاز انرژی یک فرآیند آسیاب به شدت به اندازه دستگاه فرز و کار ماشینکاری بستگی دارد.
در این مثال، یک محفظه آلومینیومی با ابعاد 150 میلیمتر در 50 میلیمتر در 25 میلیمتر قرار است بر روی یک مرکز ماشینکاری با یک پاکت کاری 850 میلیمتر در 700 میلیمتر در 500 میلیمتر آسیاب شود. میانگین کل توان مصرفی تمامی گروه های مصرف کننده فوق الذکر 13 کیلو وات برای خشن کردن و 7.4 کیلو وات برای فینیشینگ می باشد. تعادل قدرت در حین خشن کردن و تکمیل اطلاعات دقیق تری در مورد توزیع مصرف انرژی در بین گروه های مصرف کننده فردی ارائه می دهد.
روان کننده خنک کننده به صورت مرکزی و دور از ماشین فرز تهیه می شود (پمپ زدن، تثبیت دما). برای خشن کردن، این نیاز به توان متوسط 5.1 کیلو وات دارد. برای تکمیل، میانگین توان مورد نیاز به 1.5 کیلو وات کاهش می یابد. آمادگی تولید تقریباً هیچ برقی مصرف نمی کند. ماشینکاری خشک در اینجا پتانسیل زیادی برای افزایش بهره وری انرژی و منابع ارائه می دهد. با این حال، در بسیاری از کاربردهای آسیاب، انجام بدون روانکار خنک کننده می تواند میزان ضایعات را به میزان قابل توجهی افزایش دهد و در نتیجه میانگین مصرف انرژی را افزایش دهد.
میانگین توان هوای فشرده تنها در مراحل آمادهسازی تولید، خشنکاری و تکمیل اندکی تغییر میکند. میانگین آن تقریبا 1.3 کیلو وات هوای فشرده برای حداقل روانکاری دوک، تعویض ابزار و تمیز کردن قطعه کار مورد نیاز است. در مقادیر کم به عنوان هوای آب بندی (دوک، اندازه گیری ابزار، رمزگذارهای خطی) مورد نیاز است.
مصرف کننده های الکتریکی دستگاه شامل کنترل CNC با دوک اصلی و موتورهای محور تغذیه و همچنین قطعات کمکی متعدد (تغییر پالت، خنک کننده، هیدرولیک، اتوماسیون) می باشد. توان مصرفی اجزای کمکی در شرایط تولید آماده، خشن و تکمیل تنها 600 وات متفاوت است. با توان مصرفی 2.5 کیلو وات، اجزای کمکی تا حد زیادی مصرف انرژی در شرایط آمادگی تولید را تعیین می کنند. بنابراین، غیرفعال کردن اجزای کمکی مبتنی بر نیاز، صرفه جویی در انرژی بالقوه قابل توجهی را ارائه می دهد.
بسته کنترل CNC با موتورهای محور تغذیه و اسپیندل اصلی در این مثال تنها به 27 درصد از کل توان مورد نیاز نیاز دارد. در هر دو حالت، میانگین توان مصرفی موتورهای تغذیه 250 وات است و تا حد زیادی توسط قدرت نگهدارنده محور عمودی تعیین می شود. مقادیر اوج کوتاه فقط در فرآیندهای شتاب و ترمز رخ می دهد.
موتورهای اسپیندل و محور تغذیه از اجزای مرکزی یک ماشین ابزار هستند. بازده انرژی یک جزء محرک به نسبت توان تحویلی به توان مصرفی بستگی دارد و بنابراین در راندمان منعکس می شود. شبکه درایوهای یک ماشین ابزار، انرژی الکتریکی مصرف شده را به توان مکانیکی تحویلی تبدیل می کند. اجزای شبکه درایو عبارتند از یک ماژول منبع تغذیه، ماژول های درایو، موتورها و اجزای مکانیکی. داده های مربوط به راندمان معمولاً به توان نامی اشاره دارد. در سایر مقادیر رتبه بندی شده، کارایی اجزای جداگانه می تواند به طور قابل توجهی متفاوت باشد. ماژول های تامین HEIDENHAIN و ماژول های درایو به مقادیر بازدهی بیش از 95 درصد می رسند.
بهره وری انرژی اجزای درایو
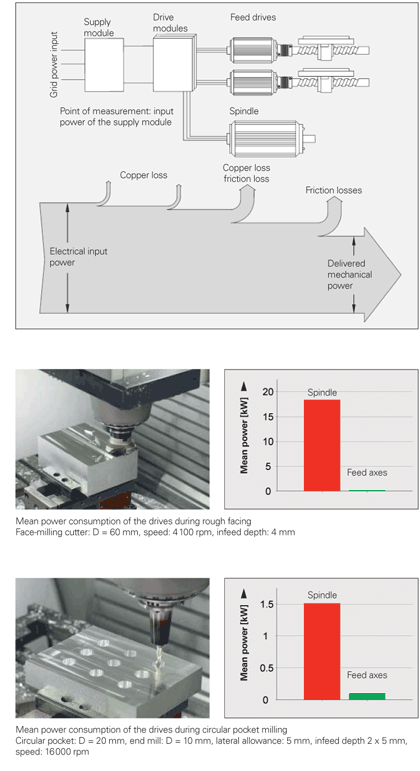
مصرف برق در هنگام آسیاب

در اینجا میزان مصرف برق یک اسپیندل اصلی و درایوهای تغذیه مشخص شده است.
مثال 1: صورت ناهموار
در هنگام مواجهه ناهموار با نرخ تغذیه پاراکسیال، موتورهای تغذیه دارای میانگین توان مصرفی 200 وات هستند. اسپیندل اصلی تقریباً به توان نامی خود می رسد. 19 کیلو وات
مثال 2: جیب دایره ای
جیب دایره ای با چرخه خشن و تکمیل ماشین کاری می شود. قدرت متوسط درایوهای تغذیه در اینجا 100 وات است. اسپیندل اصلی به 1.5 کیلو وات نیرو نیاز دارد.
نتیجه
درایوهای تغذیه تنها سهم کمی از توان کل یک CNC دارند و بنابراین می توانند سهم کمی در افزایش بهره وری انرژی داشته باشند. از طرفی انتخاب اسپیندل می تواند تاثیر بسزایی در مصرف انرژی داشته باشد. اگر یک درایو اسپیندل بسیار کمتر از توان نامی خود کار کند، تلفات ذاتی درایو به نسبت افزایش می یابد و اثرات منفی بر تعادل انرژی خواهد داشت. اگر اسپیندل حداکثر سرعت حذف فلز ممکن را در فرآیند آسیاب محدود کند، فرآیند آسیاب ناگزیر زمان بیشتری می برد. نتیجه: بازده انرژی به دلیل بار پایه تولید شده توسط اجزای کمکی کاهش می یابد. همچنین پتانسیل طراحی کارآمدتر فرآیندهای آسیاب در در نظر گرفتن راندمان موتورهای اسپیندل وجود دارد، به عنوان مثال با استفاده از موتورهای سنکرون به جای موتورهای ناهمزمان.
هر فرآیند شتاب گیری یک درایو مستلزم فرآیند ترمزگیری است. انرژی حاصل از توده های متحرک درایوها تا حد زیادی به انرژی الکتریکی تبدیل می شود.
ماژول های تامین کنترل های CNC از HEIDENHAIN هم برای ترمز احیا کننده و هم غیر احیا کننده طراحی شده اند. در یک ماژول منبع تغذیه غیر احیا کننده، انرژی جنبشی آزاد شده توسط فرآیند ترمز توسط مقاومت های ترمز به گرما تبدیل می شود. یک ماژول منبع تغذیه احیا کننده این انرژی را به شبکه برق برمی گرداند. با این حال، مسیر مورد نیاز برای بازگشت انرژی و اجزای لازم برای هموارسازی برق شبکه، حتی زمانی که درایوها نیازی به برق ندارند، تلفات ایجاد می کنند. تلفات برق حتی زمانی که برق بازسازی نمی شود کمی افزایش می یابد. یک ماژول منبع تغذیه احیا کننده زمانی کارآمدتر از یک ماژول غیر احیا کننده عمل می کند که انرژی بازسازی شده بیش از آن اتلاف توان بالاتر را جبران کند.
تعداد تغییرات ابزار برای مصرف انرژی مهم است. در یک مثال، عملیات فرز با 15 کیلووات به صورت دوره ای با تغییر ابزار قطع می شود. راه اندازی اسپیندل به حداکثر توان تقریباً نیاز دارد. 60 کیلو وات در حالی که ماژول منبع تغذیه احیا کننده به طور خلاصه 48 کیلو وات را به برق شبکه برمی گرداند، با مدول تامین غیر احیا کننده، انرژی جنبشی به گرما تبدیل می شود.
با توجه به نیاز بالای برق برای برش فلز، میانگین توان ورودی هرچه بیشتر فرآیند فرز با تغییر ابزار قطع شود، کاهش می یابد. به محض اینکه فاصله زمانی بین دو تغییر ابزار کمتر از 100 ثانیه باشد (معادل 0.6 تغییر ابزار در دقیقه) ماژول تامین احیاکننده کارآمدتر کار می کند. در فرآیندهایی با تغییرات زیادی ابزار در دقیقه، یک ماژول تامین احیا کننده اغلب ثابت میکند که انتخاب بهتری است. در طول فرز کانتور با تغییرات نادر ابزار، مزایای سیستم غیر احیا کننده است.
کارایی ماژول های تامین احیا کننده

غیرفعال کردن اجزای کمکی در صورت نیاز
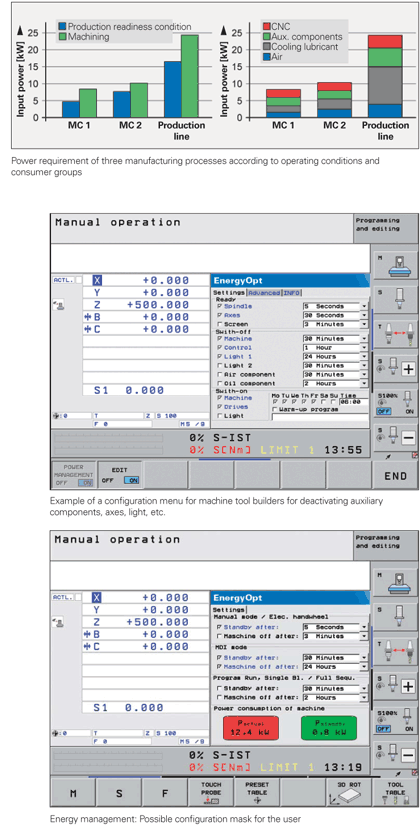
مقایسه توان مصرفی دو مرکز ماشینکاری (MC) و یک خط تولید با سه ایستگاه ماشینکاری مجدداً این پتانسیل را نشان میدهد: از آنجایی که مصرف چندین گروه مصرفکننده در شرایط آماده فقط اندکی کاهش مییابد، فازهای غیرمولد باید به طور خلاصه نگه داشته شوند. تا حد ممکن. با مراکز ماشینکاری برای دسته های تولید کوچکتر، مصرف انرژی را می توان با غیرفعال کردن انتخابی اجزای کمکی به میزان قابل توجهی کاهش داد. فراتر از این، صرفه جویی بالقوه ناشی از استفاده از پمپ های انرژی کارآمد در مدار خنک کننده / روان کننده است.
با این حال، خاموش شدن مداوم اجزای کمکی (هیدرولیک، خنک کننده دوک) یا منبع هوای فشرده نیز می تواند اثر معکوس داشته باشد. اگر حذف ناگهانی گرمای اتلاف از اجزای کمکی یا اثر تثبیت کننده دما از محیط باعث جابجایی حرارتی در قاب دستگاه شود، می تواند منجر به قطعات ضایعاتی شود که تعادل انرژی یک فرآیند تولید را مختل می کند. بنابراین، خاموش شدن انتخابی اجزای کمکی در ماشینهایی که تمایل کمی به جابجایی حرارتی دارند، بهترین عملکرد را دارد. در هر صورت، برنامه ریزی دقیق اثرات صرفه جویی در انرژی یک پیش نیاز است.
CNC را می توان به عنوان واحد کنترل مرکزی برای مدیریت انرژی یک ماشین ابزار و اطراف آن استفاده کرد. iTNC 530 با عملکردهای ویژه PLC برای پیوند دادن رویدادها در فرآیند تولید (به عنوان مثال توقف NC) با خروجی برای کنترل اجزای کمکی ارائه شده است. زمانهای تأخیر را میتوان به رویدادها اختصاص داد، بهطور مثال، موتورها را میتوان قفل کرد و پس از توقف از جریان برق جدا کرد. بر این اساس می توان عملکردهایی برای غیرفعال کردن وسایل کمکی مختلف، محورها، نور در فضای کار و ... ایجاد کرد. این توابع اساسی را می توان به دلخواه سازنده ماشین ابزار ایجاد کرد و با مدل ماشین مربوطه تطبیق داد. برای کاربر، یک مرحله بیشتر مفید است که در آن مدیریت انرژی را می توان با عادات استفاده خاص وی تطبیق داد. در مثال نشان داده شده، عملکردهای غیرفعال سازی (قفل کردن محور، آماده به کار،
به دلیل بار انرژی پایه نسبتاً بالای ماشین ابزار، زمانهای غیر برشی تأثیر تعیینکنندهای بر بازده انرژی فرآیند برش دارد. برای کاهش انرژی مورد نیاز هر قطعه، دورههای غیربرشی مانند زمان ابزار و نصب باید تا حد امکان کوچک باشد. در اصل، هر چیزی که بهره وری دستگاه را افزایش دهد، کارآمد است.
کاهش زمان بیکاری دستگاه از طریق پشتیبانی بهینه در حین راه اندازی
زمان های بدون برش در حین نصب
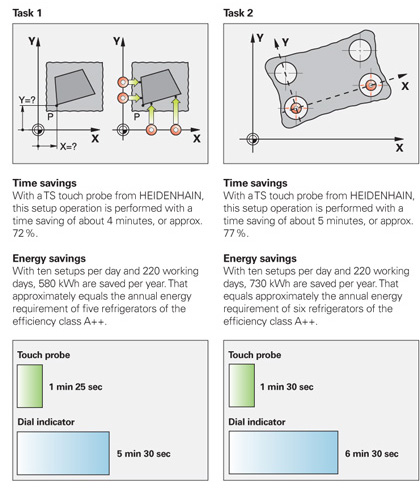
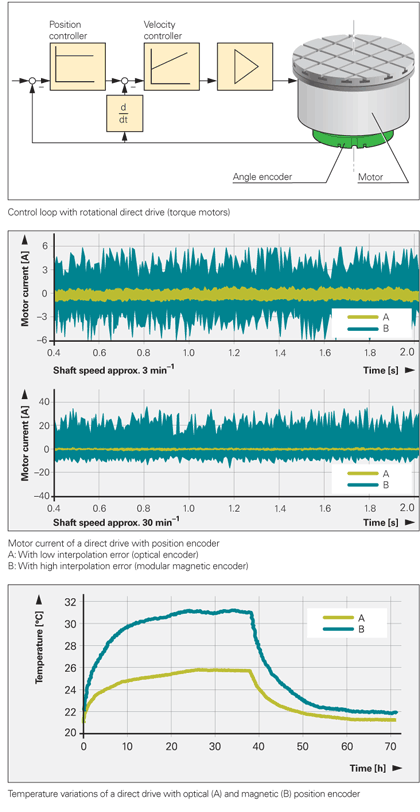
کار داده میشوند که ابتدا باید روی قطعه کار ثابت اندازهگیری شوند. یک پروب لمسی قطعه کار اندازه گیری سریع و ایمن داده ها را تضمین می کند. چرخه های از پیش تعریف شده پروب لمسی و اتصال بدون تاخیر بین پروب لمسی و کنترل به طور قابل توجهی زمان عدم برش را کاهش می دهد و در عین حال دقت ماشینکاری را افزایش می دهد. داده ها را می توان به طور خودکار با استفاده از پروب های لمسی TS در ترکیب با عملکردهای کاوشگر کنترل های TNC تنظیم کرد. این امر باعث میشود از خطاهایی در حین راهاندازی که ناگزیر منجر به ایجاد قطعات بد میشود جلوگیری شود.
پروب های لمسی می توانند زمان عدم برش را کاهش دهند، کیفیت تولید را بهبود بخشند، از ضایعات جلوگیری کنند و بهره وری را افزایش دهند. این امر انرژی مورد نیاز هر قطعه تولیدی را کاهش می دهد. در این دو مثال، امکان کاهش زمانهای برشخوردگی نشان داده شده است. در اینجا زمانهای راهاندازی با یک عدد سنج و پروبهای لمسی HEIDENHAIN روی یک ماشین ابزار با بار پایه 4 کیلو وات مقایسه میشود.
وظیفه 1
- قطعه کار را به موازات محورها تراز کنید
- داده را در صفحه کار در یک گوشه تنظیم کنید
- داده محور ابزار را در سطح بالایی قسمت خالی تنظیم کنید
وظیفه 2
- یک قطعه کار را به صورت پاراکسیال با استفاده از دو سوراخ تراز کنید
- داده صفحه کار را در مرکز اولین سوراخ تنظیم کنید
- داده محور ابزار را در سطح بالایی قسمت خالی تنظیم کنید
سیستم های اندازه گیری برای عملکرد کارآمد انرژی موتورهای سروو کنترل شده
در حلقههای کنترل موتورهای اسپیندل و محورهای تغذیه مستقیم، حتی کوچکترین اختلال در سیگنالهای بازخورد میتواند منجر به نوسانات زیادی در جریان موتور شود.
درون یابی سیگنال یک رمزگذار موقعیت شامل انحرافات برد کوتاه در یک دوره سیگنال (خطای درون یابی) است که معمولاً حدوداً حدوداً حدوداً یکسان است. 0.5٪ از دوره سیگنال. اگر فرکانس خطای درون یابی افزایش یابد، درایو تغذیه دیگر نمی تواند منحنی خطا را دنبال کند. با این حال، اجزای جریان اضافی توسط خطای درون یابی تولید می شوند. بنابراین، اگر گشتاور ثابت بماند، مصرف انرژی و راندمان موتور بدتر می شود. انرژی اضافی مورد نیاز به گرما تبدیل می شود. گرما معمولاً باید توسط یک سیستم خنک کننده موتور دفع شود که خود انرژی مصرف می کند.
مقایسه اثرات یک رمزگذار مغناطیسی نوری و یک رمزگذار مغناطیسی مدولار بر روی میز دوار با درایو مستقیم، معنای سیگنالهای موقعیت با کیفیت بالا را نشان میدهد. انکودر زاویه RCN 226 با 16 384 خط تنها اختلالات قابل توجهی را در جریان موتور ایجاد می کند و گرمای کمی ایجاد می کند. به دلیل اصل اسکن مغناطیسی، رمزگذار دارای دوره های سیگنال بسیار کمتری است. اختلالات قابل توجهی در جریان موتور با تنظیمات کنترل کننده یکسان رخ می دهد. به عنوان مثال، در سرعت شفت تقریبا. 30 دقیقه–1 مقدار موثر جریان 15 A بیشتر از یک رمزگذار نوری است. نتیجه تولید گرمای بیشتر در موتور است.
یک رمزگذار با کیفیت سیگنال پایین می تواند منجر به اتلاف انرژی بیشتر در موتورها شود. علاوه بر این، انرژی اضافی مورد نیاز خنک کننده فعال باید در تراز انرژی لحاظ شود. برای افزایش بازده انرژی موتور، انکودرها باید دارای کیفیت سیگنال بالایی باشند.
قطعات بد بهره وری یک فرآیند تولید را کاهش می دهند و بنابراین تا حد زیادی به هزینه های انرژی برای هر قطعه ساخته شده کمک می کنند. یکی از دلایل اصلی تولید قطعات بد، رانش حرارتی محورهای تغذیه است که بر روی بال اسکروهای چرخشی کار می کنند.
توزیع دما در امتداد پیچ های توپی را می توان به سرعت توسط نرخ تغذیه و نیروهای متحرک تغییر داد. در ماشین ابزار در یک حلقه نیمه بسته (یعنی بدون رمزگذارهای خطی، شکل 1 بالا) تغییرات در طول (معمولا: 100 میکرومتر بر متر در 20 دقیقه) می تواند باعث نقص های قابل توجهی در قطعه کار شود.
اگر از یک رمزگذار خطی برای اندازه گیری موقعیت لغزش استفاده شود (شکل 1، زیر)، افزایش دمای بال اسکرو (شکل 2) تأثیری بر دقت ندارد. این به عنوان عملیات در یک حلقه بسته شناخته می شود زیرا خطاهای مکانیکی درایو در حلقه کنترل موقعیت اندازه گیری می شود و بنابراین جبران می شود.
به حداقل رساندن ضایعات از طریق فناوری حلقه بسته
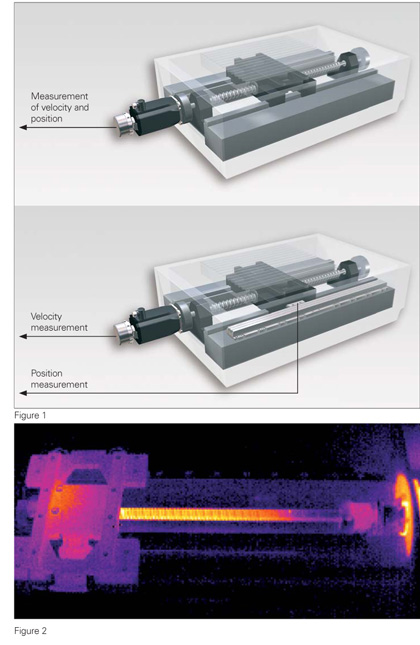
صرفه جویی در انرژی در یک حلقه بسته
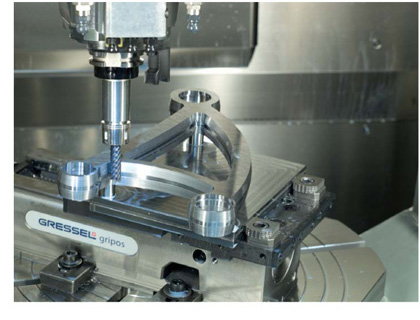
ساخت 22 اهرم کوپلینگ 2 ساعت طول می کشد. سوراخ دو سوراخ در فاصله 350 میلی متری باید با تلرانس IT7 ساخته شود که خطای 28 ± میکرومتر را ممکن می کند. برای تولید 22 قطعه خوب در یک حلقه نیمه بسته، ابتدا دستگاه باید برنامه NC را به صورت دوره ای به مدت 25 دقیقه اجرا کند تا از تطابق با تلورانس IT7 اطمینان حاصل شود. در حین گرم کردن، مصرف انرژی تقریباً تقریباً است. 10 درصد کمتر از مقدار برای آسیاب.
در نتیجه، هزینه انرژی هر قطعه خوب در حلقه نیمه بسته، 19 درصد بیشتر از ساخت 22 قطعه در یک حلقه بسته با رمزگذارهای خطی است. اگر 50 قطعه بر روی یک ماشین فرز در حلقه نیمه بسته با فاز گرم کردن قبلی ساخته شود، نیاز به انرژی در طول آسیاب 8 کیلو وات در 220 روز کاری برای انرژی اضافی 660 کیلووات ساعت ایجاد می شود.
نتیجه
تجزیه و تحلیل فرآیندهای برش فلز نشان می دهد که مصرف برق یک کنترل CNC با محور تغذیه و موتورهای اسپیندل اغلب تنها 25 تا 30 درصد از کل توان مورد نیاز را شامل می شود. از سوی دیگر، اجزای کمکی موجود در ماشین یا محیط آن نقش غالبی در تعادل انرژی دارند.
امکانات متعددی برای استفاده کارآمدتر از انرژی وجود دارد. صرفه جویی قابل توجهی را می توان از طریق انتخاب مناسب قطعات برای یک ماشین ابزار به تنهایی محقق کرد. اینکه یک کنترل CNC باید دارای بازیابی انرژی به توان خط باشد یا خیر، به فرکانس تعویض ابزار در حین عملیات فرزکاری یا تغییر قطعه کار در حین تراشکاری بستگی دارد. سپس انرژی بازسازی شده برای سایر مصرف کنندگان در محیط ماشین در دسترس است.
صرفه جویی بیشتر در مصرف انرژی بسته به این که آیا دوک ها می توانند از نظر سرعت و گشتاور با محدوده عملکرد ماشین سازگار شوند یا نه، امکان پذیر است. اگر طراحی جهانی دوک مورد نیاز باشد، موتور اسپیندل ممکن است باید با نرخ بازده پایین کار کند - با عواقب مورد انتظار برای مصرف انرژی.
انتخاب انکودر موقعیت میتواند تأثیر تعیینکنندهای بر کارایی موتورهای اسپیندل و درایوهای مستقیم داشته باشد. رمزگذارهایی با وضوح و دقت ناکافی مقادیر جریان بالایی را در حلقه کنترل موقعیت تولید می کنند. رمزگذارهای موقعیت با تعداد خطوط بالا برای راندمان بالای درایوهای کنترل شده با سروو ضروری هستند. ثابت شده است که رمزگذارهای خطی دقت را افزایش می دهند و بنابراین به دقت و تکرارپذیری بالاتر نتایج ماشینکاری کمک می کنند. این امر کاهش ضایعات در تولید و در نتیجه فوری انرژی مورد نیاز هر قطعه خوب را ممکن می سازد.
قطعات برای پردازش روان کننده های خنک کننده، برای تامین هوای فشرده و هیدرولیک و برای خنک کننده سهم غالبی از کل توان را به خود اختصاص می دهند. اگر ماشینی دارای موتورهای پمپ کارآمد باشد، این به تنهایی می تواند مقادیر قابل توجهی انرژی را ذخیره کند. فرصت دیگری با مدیریت انرژی در کنترل CNC با خاموش کردن انتخابی قطعات ارائه شده است. به عنوان مثال، این امکان را فراهم می کند که خاموش شدن درایوهای پمپ را پس از پایان عملیات ماشینکاری به تاخیر بیندازید.
حتی در خود فرآیند تولید نیز می توان به صرفه جویی در مصرف انرژی پی برد. با بار پایه نسبتاً بالای ماشین ابزار، کاهش فازهای غیرمولد اولویت بالایی دارد. در اینجا کنترلهای CNC از HEIDENHAIN میتوانند به طرق مختلف کمک کنند. با شروع ایدههایی برای ویرایش برنامههای کاربرپسند تا عملکردهایی برای راهاندازی قطعه کار با سیستمهای کاوشگر لمسی HEIDENHAIN، تا کنترل حرکتی کارآمدتر و دقیقتر در ماشینکاری سه و پنج محور، کاربران از دانش جمعآوریشده توسط HEIDENHAIN سود میبرند. با چندین دهه تجربه در تکنولوژی برش فلز.